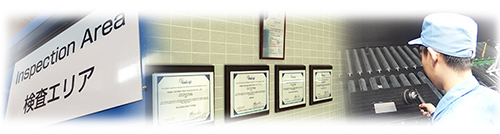
For enhancing international competitiveness of the manufacturing industry, improving QCD (Quality, Cost, Delivery) is important. We are focusing on mastering various technologies for establishing an integrated production (consistent processing) system. This time, we will focus on and feature "Nondestructive testing in the field of aerospace products" .
Nondestructive testing is an inspection method that investigates presence, position, size, shape, etc. of flaws without destroying materials or products. In the field of aerospace, it is mandatory to conduct nondestructive testing. Various types of inspection methods are included in the nondestructive testing, such as penetrant testing, ultrasonic testing, eddy current testing, magnetic particle testing, and radiography testing, and a method that suits best to application and properties of a product to be tested is selected.
- 拡大
- MP Solutions-Chubu Department
Deputy General Manager
Shuichi Osako
Komaki plant, MP Solutions-Chubu Department conducts the penetrant testing among these inspection methods. In the penetrant testing, in order to enlarge flaws, liquid (penetrant) that has a good penetrability and in a vivid or a fluorescent color is applied to materials to penetrate into the flaws and then drawn out to a surface of the materials. This inspection method allows the inspector to find out micro-cracks or the like that cannot be seen with naked eyes.
MP Solutions-Chubu Department stably supplies high quality products without any discontinuities by applying the penetrant testing to inspection of aircraft engine parts such as turbine blades.
In order to conduct the nondestructive testing on aerospace products, it is necessary to pass qualification tests based on overseas standards such as NAS 410 (USA) and EN 4179 (Europe) to acquire a qualification. In addition, a supplier level 3 qualification is also required to acquire an authority to operate the nondestructive testing system from every prime contractor*1 of each product.
The qualification is divided into three levels from level 1 to level 3 depending on years of experience and skill level, and a person having level 3 qualification is essential to operate and maintain the nondestructive testing system. Therefore, in order to develop level 3 qualified inspectors, we dispatched our technicians to overseas certification bodies. As a result of taking theoretical instructions, practical trainings, and the qualification examinations, they acquired the above two qualifications.
This allowed us to have an authority to operate in-house qualification authorization for the nondestructive testing by appointing the level 3 qualified personnel as Responsible Level 3 based on NAS 410, EN 4179, and customer's certification specifications.
With the authority, while daily operation in our facility, young inspectors can gain experience time, improve their skills by receiving guidance from experienced inspectors, take an in-house qualification examination when they meet the examination requirements, and can acquire an certification of each level when they pass the examination. This facilitates the development and qualification authorization of inspectors.
- 拡大
- MP Solutions-Chubu Department
Chubu Quality Management
Group Leader
Noboru Endo
The nondestructive testing is one of special processes*2such as electric discharge machining, heat treatment, coating, and surface treatment. In order to apply the nondestructive testing to aerospace products, acquisition of Nadcap (National Aerospace and Defense Contractors Accreditation Program) accreditation is obliged by each prime contractor in addition to conformity to standards dedicated to aerospace products (JIS Q9100, NAS 410 etc.)
Since Nadcap is an international accreditation system, English is basically used in documents and audits. Therefore we prepared documents such as quality control manuals, work procedure manuals, checklists, facility management manuals, etc. in English in about one year for starting production of turbine blades. An examination for conformity to requirements of the aerospace industry was conducted by PRI (audit agency) on contents of the manuals, workers skill, compliance with the work procedures, maintenance and management situation of the facility, and so on, and we successfully acquired the Nadcap certification.
In order to conduct the penetrant testing, equipment for performing a series of processes such as pre-cleaning, penetration processing, removal processing, development processing, acceptance determination, post-cleaning is necessary. Currently, Komaki plant has two penetrant testing facilities, an automatic line and a manual line. The automatic line testing facility is automated with robotic devices. Since a series of processes from the pretreatment to the development processing is automated in a flow process, the inspectors can focus on a determination work only, therefore this facility is suitable for mass production.
An automatic line testing system using this facility has been certified by Rolls-Royce and is actively used in the nondestructive testing of the turbine blades. In contrast, in the manual line testing facility, almost all the tests are conducted by the inspectors manually. The manual line testing facility is highly versatile since the tests can be applied to parts in various sizes and shapes, and a type of the penetrant to be used can be changed depending on the parts to be tested. Our penetrant testing facilities have already been certified by Rolls-Royce and Pratt & Whitney, and conduct the nondestructive testings on parts associated with compressors and combustors for the companies.
Currently, a future demand forecast for commercial aircraft engine business, which MP Solutions-Chubu Department is working on, is expected to grow continuously over a long period of time. For expanding the business, it is necessary to further enhance product competitiveness, therefore cost reduction and lead time shortening are required. In order to achieve this, we believe it is essential to shift from a conventional "saw type production system" in which each company conducts each process such as machining, welding, heat treatment, and so on separately, to an "integrated production system" in which a core company integrates the each process. It is extremely difficult to achieve the integrated production system by a single company alone, so industrial clusters where each company specializing in each process works in collaboration is formed in various places.
The production of the turbine blades is an example of the industrial cluster. As the core company, we are operating a system that guarantees supply and quality. The nondestructive testing is a process that must always be carried out in the consistent processing of the aerospace products, but acquisition of the accreditation including obtaining the inspector qualifications and passing the Nadcap examination, etc. are extremely difficult. Therefore, a fact that we already have these accreditation and certifications is a huge advantage in developing the cluster business. We will continue to strive to maintain and improve our nondestructive testing technology, and will respond to customer's needs by continuing to provide stable and high quality products. In addition, we will challenge products in new fields with advantage of our possession of the accreditation and the various certifications.
*1 Prime contractor:
A company (such as an aircraft manufacturer, an engine manufacturer) having original design rights and parts ordering rights.
*2 Special Process:
A process in which a product cannot be confirmed if it meets required quality standards in post-process inspections and tests.
We conduct various nondestructive testings mainly in the gas turbine field and an aircraft engine parts field. We will continue to strive to acquire new technologies for establishing the higher level of integrated production (consistent processing) system.
|